- CSCD核心中文核心科技核心
- RCCSE(A+)公路运输高质量期刊T1
- Ei CompendexScopusWJCI
- EBSCOPж(AJ)JST
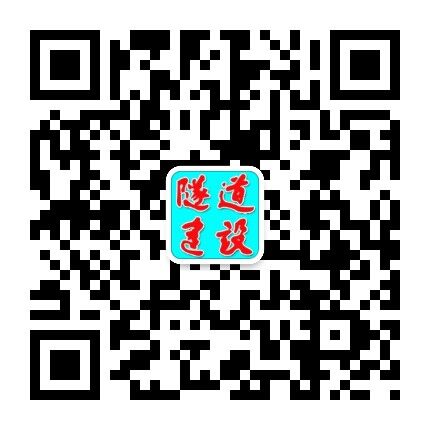
隧道建设(中英文) ›› 2024, Vol. 44 ›› Issue (5): 1086-1095.DOI: 10.3973/j.issn.2096-4498.2024.05.016
高水压下微裂隙竖井井底车场硐室堵水注浆施工关键技术——以大瑞铁路高黎贡山隧道1#竖井为例
高广义, 翟康博, 谷晴天
Key Technology for Water Blocking and Grouting Construction in Chamber of Bottom Car Yard of Microcrack Vertical Shafts Under Extremely
High Water Pressure: A Case Study of Vertical Shaft No. 1 of Gaoligongshan Tunnel on DaliRuili Railway
GAO Guangyi, ZHAI Kangbo, GU Qingtian
摘要: 为有效解决极高水压下微裂隙狭小硐室安全掘进中突水淹井的施工难题,依托大瑞铁路高黎贡山隧道1#竖井井底车场硐室超前堵水施工,针对竖井极高水压(7.6 MPa),地层蒙脱石含量高、可注性差,井底排水能力有限,注浆堵水难度大、要求高等特点,在钻注设备选型配套和设备拆卸吊装、极高水压防突措施、超前堵水启动和结束标准制定等方面进行现场试验研究与应用,得出以下结论: 1)提出极高水压下微裂隙深大竖井井底车场超前堵水注浆“合理步距、封堵水流;由外到内、环环相扣;间隔跳孔、锁定水源;增加补孔、局部加强”的原则; 2)定制大功率窄体履带式液压钻机并配置无级变速超高压低流量双液泵,满足狭小空间钻机反复拆、吊快速安全施工; 3)采用溶液型的改性脲醛树脂,以2~3倍静水压力作为注浆终压,有效解决了地层可注性差的问题,达到了较好的堵水效果; 4)通过原位压水试验预测前方涌水量并结合井内实际抽排能力,明确“以堵为主、限量排放”的治水原则,利用钻孔压水试验计算渗透系数并以此来制定超前注浆启动标准,以达到注浆效果的渗透系数确定堵水结束标准; 5)确定注浆最优循环长度为25 m,综合施工效率达到最高。