- CSCD核心中文核心科技核心
- RCCSE(A+)公路运输高质量期刊T1
- Ei CompendexScopusWJCI
- EBSCOPж(AJ)JST
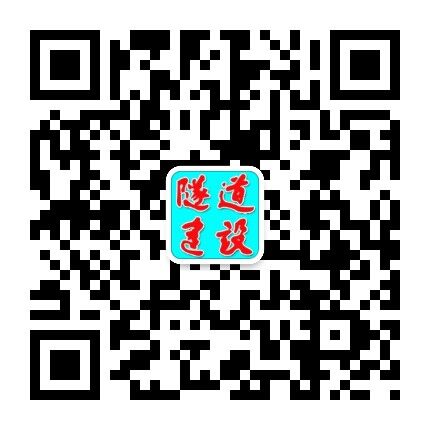
隧道建设(中英文) ›› 2021, Vol. 41 ›› Issue (S2): 360-366.DOI: 10.3973/j.issn.2096-4498.2021.S2.046
贾文顺1 , 朱晔1,*, 王玉任2, 杜成龙1, 雷蕾1
Prediction of Fatigue and Service Life of Welded Structure of Tunnel Boring Machine Cutterhead
JIA Wenshun1, ZHU Ye1, *, WANG Yuren2, DU Chenglong1, LEI Lei1
(1. School of Mechanical Engineering, Dalian Jiaotong University, Dalian 116028, Liaoning, China; 2. Dalian Mingyang Technology Industrial Co., Dalian 116045, Liaoning, China)
摘要: 为能够准确预测全断面隧道掘进机(TBM)刀盘筋板焊接区域的疲劳寿命,以疲劳累积损伤为理论基础,采用缺口应力法对焊接区域进行疲劳寿命研究。首先,在误差允许范围内对刀盘进行简化建模,简单分析刀盘工况,并编程简化获得外部激励载荷;其次,分析缺口应力法在刀盘焊接结构上的适应性,对刀盘整体进行瞬态动力学仿真确定危险区域为筋板位置,采用虚拟缺口半径法建立TBM刀盘筋板模型,从而更好地体现焊缝处的细节特征,随后进行子模型仿真分析,将结果中焊根处的应力作为疲劳评估的参考应力;最后,基于修正的S-N曲线结合修正的平均应力保守估算焊接结构的寿命。结果显示: 1)采用缺口应力法可以精确预测刀盘的疲劳寿命,筋板的疲劳寿命在其焊根处最小N=2.326×107,经计算刀盘掘进距离约为21.9 km时,焊缝处将率先发生疲劳破坏,所得计算结果与实际情况相近; 2)TBM在掘进过程中刀盘焊接区域容易出现不同程度的疲劳损伤,导致TBM提前失去工作能力,造成工程上大量不必要的损失,研究刀盘焊接疲劳寿命对工程施工及结构改进具有重要的意义。