- CSCD核心中文核心科技核心
- RCCSE(A+)公路运输高质量期刊T1
- Ei CompendexScopusWJCI
- EBSCOPж(AJ)JST
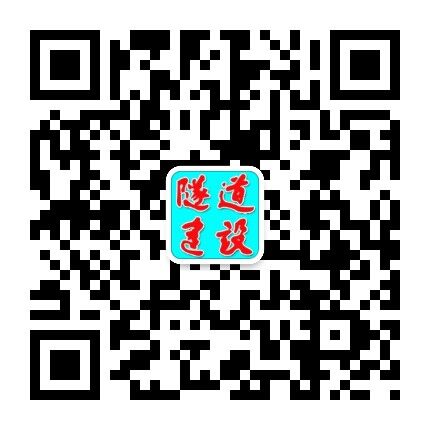
隧道建设(中英文) ›› 2024, Vol. 44 ›› Issue (10): 2094-2102.DOI: 10.3973/j.issn.2096-4498.2024.10.018
刘四进1, 马浴阳1, 2, *, 王华伟1, 王军1, 2, 3, 薛峰1, 魏英杰1, 2, 喻星乔1
(1. 中铁十四局集团有限公司, 山东 济南 250101; 2. 中国铁建水下隧道工程实验室, 山东 济南 250101;3. 东南大学网络空间安全学院, 江苏 南京 211189)
Design and Analysis of a Novel Cutter System for a Cutter-Changing Robot in Tunnel Boring Machines
LIU Sijin1, MA Yuyang1, 2, *, WANG Huawei1, WANG Jun1, 2, 3, XUE Feng1,
WEI Yingjie1, 2, YU Xingqiao1
1. China Railway 14th Bureau Group Corporation Limited, Jinan 250101, Shandong, China; 2. China Railway Construction Underwater Shield Tunnel Engineering Laboratory, Jinan 250101, Shandong, China; 3. School of Cyber Science and Engineering, Southeast University, Nanjing 211189, Jiangsu, China)
摘要: 为解决TBM掘进过程中传统滚刀换刀周期长、安全隐患大等问题,研制一种可用于机器人更换滚刀的新型刀具系统并对其进行动力学分析。采用牛顿第二定律和集中质量参数法建立新型刀具系统的动力学微分方程,并利用Newmark数值方法进行求解,分析系统各构件响应规律; 设计并开展新型刀具系统缩尺样件振动试验,验证新型刀具系统在实际破岩时的动力学行为,进行基于实测载荷的系统动态响应分析。研究结果表明: 1)滚刀的理论与试验垂向振动位移均值相对误差为9.99%,刀箱的理论与试验垂向振动位移均值相对误差为5.18%,验证了所建立的系统垂向动力学模型的正确性; 2)实际载荷下系统振动均方根值和幅值最大值分别为0.230 mm和0.700 3 mm,为预测系统在实际破岩时的动力学行为提供理论依据。