ISSN 2096-4498
CN 44-1745/U
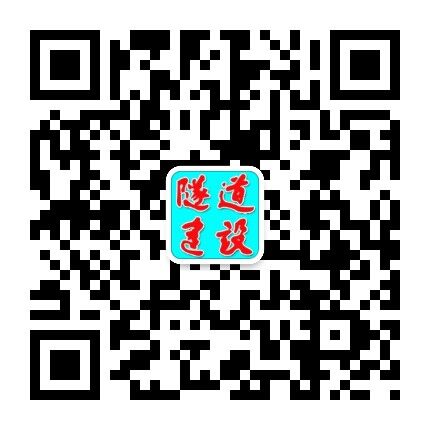
ISSN 2096-4498
CN 44-1745/U
Tunnel Construction ›› 2021, Vol. 41 ›› Issue (S2): 360-366.DOI: 10.3973/j.issn.2096-4498.2021.S2.046
Previous Articles Next Articles
Prediction of Fatigue and Service Life of Welded Structure of Tunnel Boring Machine Cutterhead
JIA Wenshun1, ZHU Ye1, *, WANG Yuren2, DU Chenglong1, LEI Lei1
(1. School of Mechanical Engineering, Dalian Jiaotong University, Dalian 116028, Liaoning, China; 2. Dalian Mingyang Technology Industrial Co., Dalian 116045, Liaoning, China)