ISSN 2096-4498
CN 44-1745/U
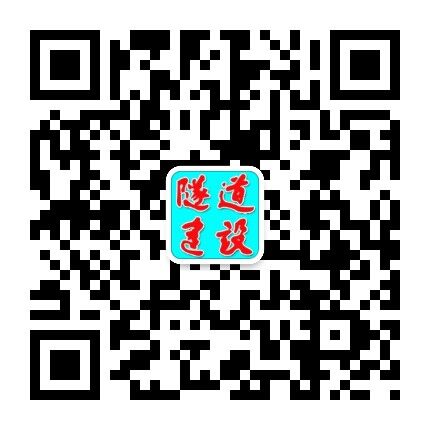
ISSN 2096-4498
CN 44-1745/U
Tunnel Construction ›› 2020, Vol. 40 ›› Issue (9): 1300-1306.DOI: 10.3973/j.issn.2096-4498.2020.09.008
Previous Articles Next Articles
WANG Xulong1, 2, ZHU Ye1, *
(1. School of Mechanical Engineering, Dalian Jiaotong University, Dalian 116028, Liaoning, China; 2. School of Automobile and Transportation, Tianjin University of Technology and Education, Tianjin 300222, China)