ISSN 2096-4498
CN 44-1745/U
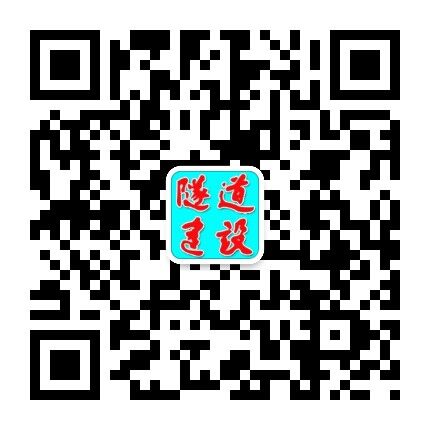
ISSN 2096-4498
CN 44-1745/U
Tunnel Construction ›› 2023, Vol. 43 ›› Issue (12): 2122-2132.DOI: 10.3973/j.issn.2096-4498.2023.12.014
Previous Articles Next Articles
Fault and Fracture Zone Collapse Treatment Technology for Open Tunnel Boring Machine Applied in Beijiang Water Diversion Project
CHEN Songlin1, WANG Lichuan2, 3, 4, HU Hengqian1, 5, WANG Shuying3, 6, 7, *,
YANG
Zebin3, 6, CHONG Panpan1,
LU Chuang1, CHEN Hongwei1
(1. China Railway 18th Bureau Group Tunnel Engineering Co., Ltd., Chongqing 400700, China; 2. China Railway 18th Bureau Group Co., Ltd., Tianjin 300222, China; 3. School of Civil Engineering, Central South University, Changsha 410075, Hunan, China; 4. School of Civil Engineering, Southwest Jiaotong University, Chengdu 610031, Sichuan, China; 5. School of Civil Engineering, Tianjin University, Tianjin 300072, China; 6. Tunnel and Underground Engineering Research Center of Central South University, Changsha 410075, Hunan, China; 7. Hunan Provincial Key Laboratory for Disaster Prevention and Mitigation of Rail Transit Engineering Structures, Central South University, Changsha 410075, Hunan, China)