ISSN 2096-4498
CN 44-1745/U
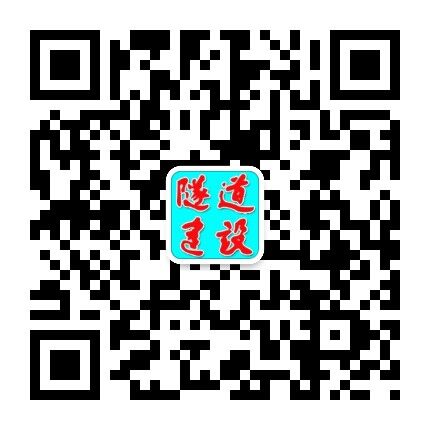
ISSN 2096-4498
CN 44-1745/U
Tunnel Construction ›› 2025, Vol. 45 ›› Issue (1): 209-220.DOI: 10.3973/j.issn.2096-4498.2025.01.018
Previous Articles Next Articles
Excavating Visualization System of a Cantilever Excavator Based on a Multi-Sensor Combined System
WEN Chengyong1, 2, YING Zongquan1, 2, *, WANG Dong3, XIE Jun3
(1. CCCC Fourth Harbor Engineering Institute Co., Ltd., Guangzhou 510230, Guangdong, China; 2. Key Laboratory of Environment and Safety Technology of Transportation Infrastructure Engineering, CCCC, Guangzhou 510230, Guangdong, China; 3. The Fourth Engineering Company of CCCC Fourth Harbor Engineering Co., Ltd., Chengdu 610213, Sichuan, China)