ISSN 2096-4498
CN 44-1745/U
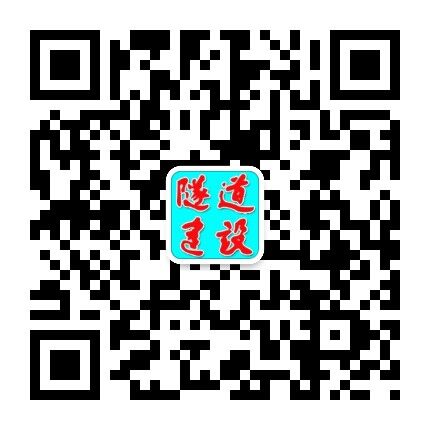
ISSN 2096-4498
CN 44-1745/U
Tunnel Construction ›› 2025, Vol. 45 ›› Issue (2): 304-314.DOI: 10.3973/j.issn.2096-4498.2025.02.006
Previous Articles Next Articles
LI Dawei1, ZHONG Xiaochun2, LIU Chang2, *, SHEN Guili1, ZHONG Jianling2, HUANG Siyuan2