ISSN 2096-4498
CN 44-1745/U
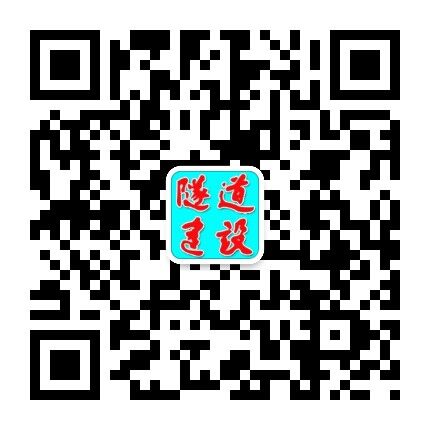
ISSN 2096-4498
CN 44-1745/U
Tunnel Construction ›› 2023, Vol. 43 ›› Issue (5): 847-855.DOI: 10.3973/j.issn.2096-4498.2023.05.012
Previous Articles Next Articles
Innovation and Practice of Key Technologies for Immersed Tunnel Terminal Joint Based on Friction Antithrust
ZENG Bocun1, FENG Jiangdong1, ZHOU Xingtao2, *, WANG Cong1, 3, SUN Xiaowei1, REN Yaopu4
(1.CCCC Second Harbour Engineering Co.,Ltd.,Wuhan 430040,Hubei,China;2.School of Civil Engineering and Architecture,Hubei University of Arts and Science,Xiangyang 441053,Hubei,China;3.Key Laboratory of Large-span Bridge Construction Technology of Ministry of Communications,Wuhan 430040,Hubei,China;4.CCCC Highway Consultants Co.,Ltd.,Beijing 100088,China)